コラム
COLUMN
製品名:EXEX生産管理
連載コラム13 スケジューラー(APS)の機能(1)
前回は、MPS、MRP、CRP(以下便宜的にこれらをまとめてMRPと呼びます)といった生産管理システムに含まれることが多い計画系機能の概要とその限界についてお話しました。今回から数回にわたり、それらの限界を解消しているソフトウェアであるスケジューラー、英語圏ではAPS(Advanced Planning and Scheduling)と呼ばれるソフトウェアの一つの代表的な製品であるASPROVAを用いて検証実験をしながら、前回指摘した問題がスケジューラーでどのように解消されているのか具体例を示しながらお話致します。なお、スケジューラーは通常、生産管理システムに含まれる機能ではなく独立したソフトウェアであり、各社のERPや生産管理システムと連携して用いるケースが大多数です。
検証実験で使うBOM
今回の実験で使用するBOMを以下に示します。
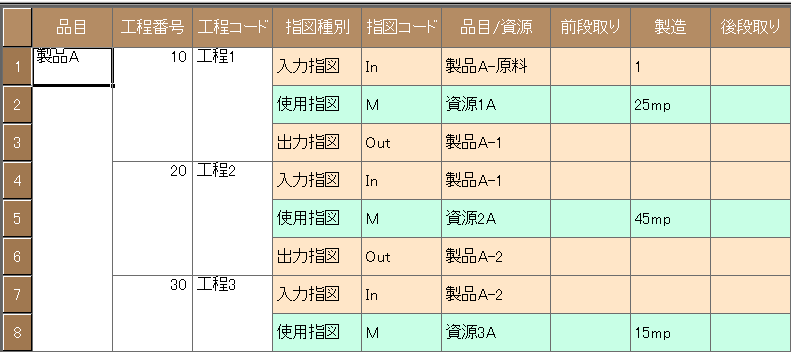
製品Aは工程1、工程2、工程3の3工程あり、それぞれ資源1A、資源2A、資源3Aという機械を使います。また工程1は1個あたり25分、工程2は1個あたり45分、工程3は1個あたり15分かかるという設定にしてあります。
「MRPではリードタイムは生産数量によらず固定である」という問題点の解消
百聞は一見にしかずでしょうから、ASPROVAを使って実験をしてみます。同じ製品の100個と200個のオーダーを登録した際の工程の作業時間計算結果を確認しましょう。
<実験1>まず製品Aの100個のオーダーを登録

スケジュール結果
実験1のガントチャート

実験1の工程の作業時間

<実験2>製品Aのオーダー200個登録

スケジュール結果
実験2のガントチャート
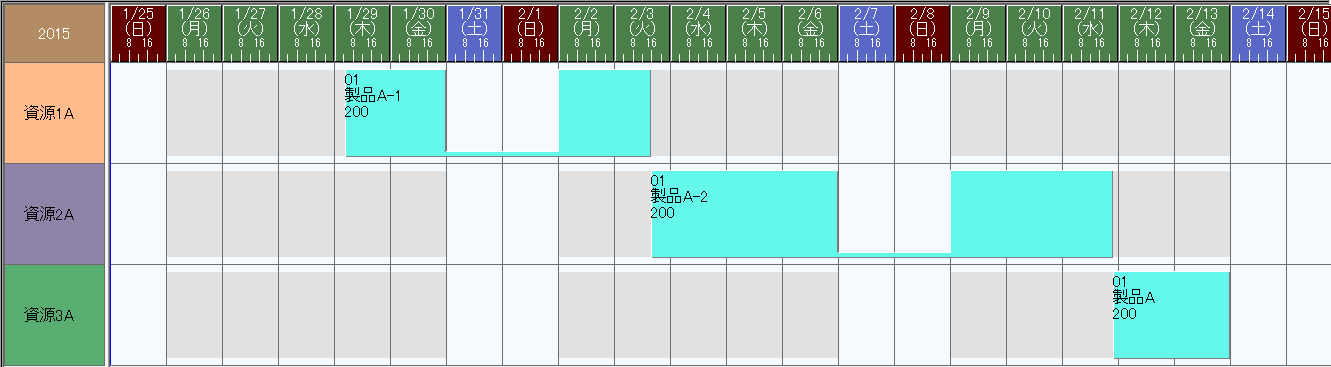
実験2の工程の作業時間

各工程の製造時間を比較してみると、オーダー数200の場合はオーダー数100の場合のそれぞれ2倍になっていることが確認できます。
このように、ASPROVAでは製造リードタイムはオーダー数量に応じて変わるものとしてスケジュール計算をします。つまり、「リードタイムは生産数量によらず固定である」という問題はASPROVAでは解消されています。
「MRPでは無限山積みをしてしまう」という問題の解消
今度は同じ納期で数量100の2つのオーダーを登録してみます。
<実験3>製品Aの同一納期のオーダー数100のオーダーを2つ登録

スケジュール結果
実験3のガントチャート

オーダー01の割付結果は水色 オーダー02の割付結果は紫色
上図のガントチャートで明らかなように、ASPROVAはたとえ同一納期のオーダーが複数あったとしても、同時に同じ機械に作業を割り付けたりはしません。つまり「無限山積みをしてしまう」という問題は解消されています。ASPROVAでは割り付けられる資源を探してから作業の割付を行うためです。なお、どのオーダーを優先して割り付けるかはオーダーの優先順位設定やその他のパラメータ指定で任意に変更可能です。
「MRPでは納期変更は前倒ししかできない」という問題の解消
<実験4>実験3のオーダー02の工程2の完了日を後ろにずらす

ASPROVAでは納期をずらす際、ガントチャート上でずらしたい工程をドラッグ&ドロップの直感的な操作で可能です。上図がオーダー02の工程2の納期を後ろにずらした状態です。
スケジュール結果
実験4のガントチャート

工程2の変更に伴い、前後の工程1、工程3の日程も変更されました。
このようにASPROVAでは任意の工程を前倒し、後ろ倒しのいずれにも自由に変更でき、つながりのある前後の工程も同期されて自動的に日程変更がされます。つまり、「MRPでは納期変更は前倒ししかできない」という問題は解消されています。また、納期を後ろにずらすことにより、最終工程の納期に遅延が出る場合はオーダーが赤字で表示されアラームが出ます。納期遅延のオーダーと工程の詳細は別画面から簡単に見つけ出し詳細を下図のように表示もできます。

「MRPでは代替設備への振替が得意ではない」という問題の解消
<実験5>工程2が資源2A、資源2Bの2台で行えるように設定しなおして、実験3と同じ条件でスケジュールしてみます。
上図のように資源2Aと資源2Bが同じ資源2Gというグループに属すように設定。
工程2で使用する資源を資源2Gに設定しなおします。
このように設定をしなおしてから、実験3と同じオーダーを登録します。
スケジュール結果
実験5のガントチャート
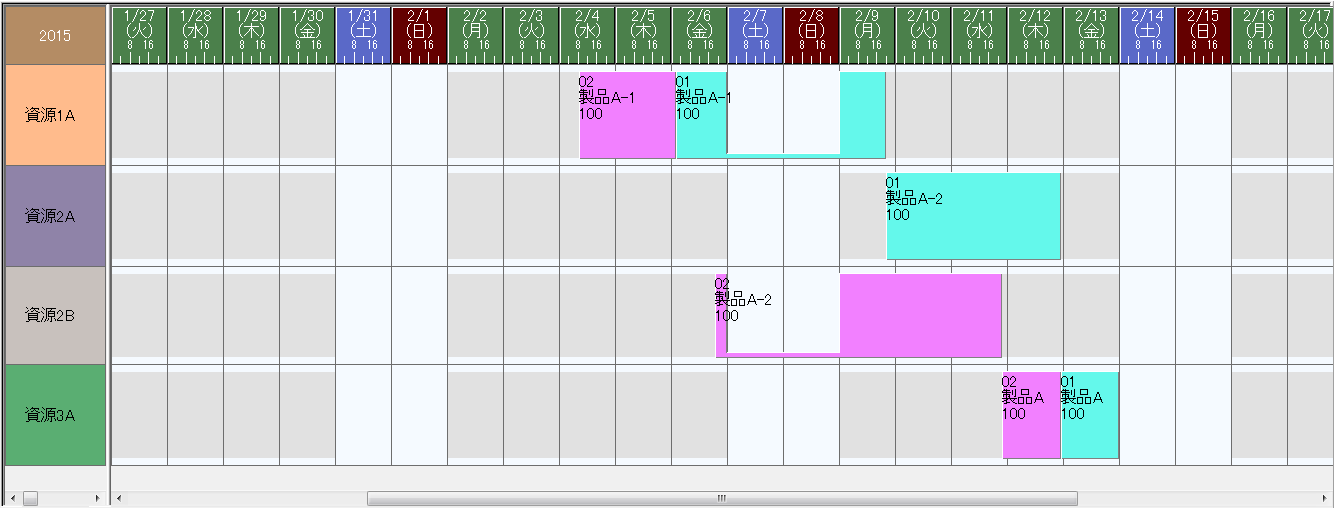
上図のように工程2は同じ時簡帯に資源2Aと資源2Bに同時に割り付けられています。つまり「MRPでは代替設備への振替が得意ではない」という問題は解消されています。
「MRPでは作業分割が得意ではない」という問題の解消
<実験6>実験5のBOMで工程2のロットサイズを50個に設定してみます。

この状態で実験5と同じオーダーのスケジューリングをしてみます。
スケジュール結果
実験6のガントチャート

上図のように工程2は50個×4つの作業に分割されました。その結果、工程全体のリードタイムが短縮しています。つまり「MRPでは作業分割が得意ではない」という問題は解消されています。適正ロットサイズを見つけるのはなかなか難しい計算が必要ですが、ASPROVAではソフトウェアでのシミュレーションで簡単に適正ロットサイズを判断することも支援します。
「計画を2段階で行う」問題の解消
MPS、ラフカットプランニング、MRP、CRPの計画作成手順は、
- (1)エンドアイテムだけの生産計画後、重要資源だけに着目してラフカットプランニングを行い
- (2)MRP実行後、全工程の負荷をチェックしCRPで山崩し
という2段階の調整手順が入りました。
しかし、これまでの例でもお分かりになると思いますが、ASPROVAでは1回のスケジューリングで一気通貫で全ての資源の負荷が能力以上になることがないように計画を作成してしまいます。また、計画作成後に特定のオーダーの特定の工程だけを納期変更後に再度スケジューリングすると全ての工程が同期をとって再スケジューリングされます。つまり「計画を2段階で行う」という問題は解消されています。
スケジューラーの機能説明は次回の稿に続きます。