導入事例
CASE
導入製品名:EXEX生産管理
システムのリニューアルを機にクラウド&タブレットを導入。
生産現場のリアルタイム状況共有が可能に。
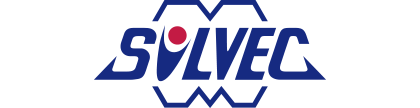
株式会社シルベック様
事業内容 | 各種部品へのメッキ加工、化成処理 |
---|---|
所在地 | 埼玉県八潮市浮塚879-3 |
設立 | 1963年10月 |
資本金 | 5500万円 |
従業員数 | 51名 |
リアルタイムの進捗管理が課題に 決め手はコスト、クラウド、タブレット
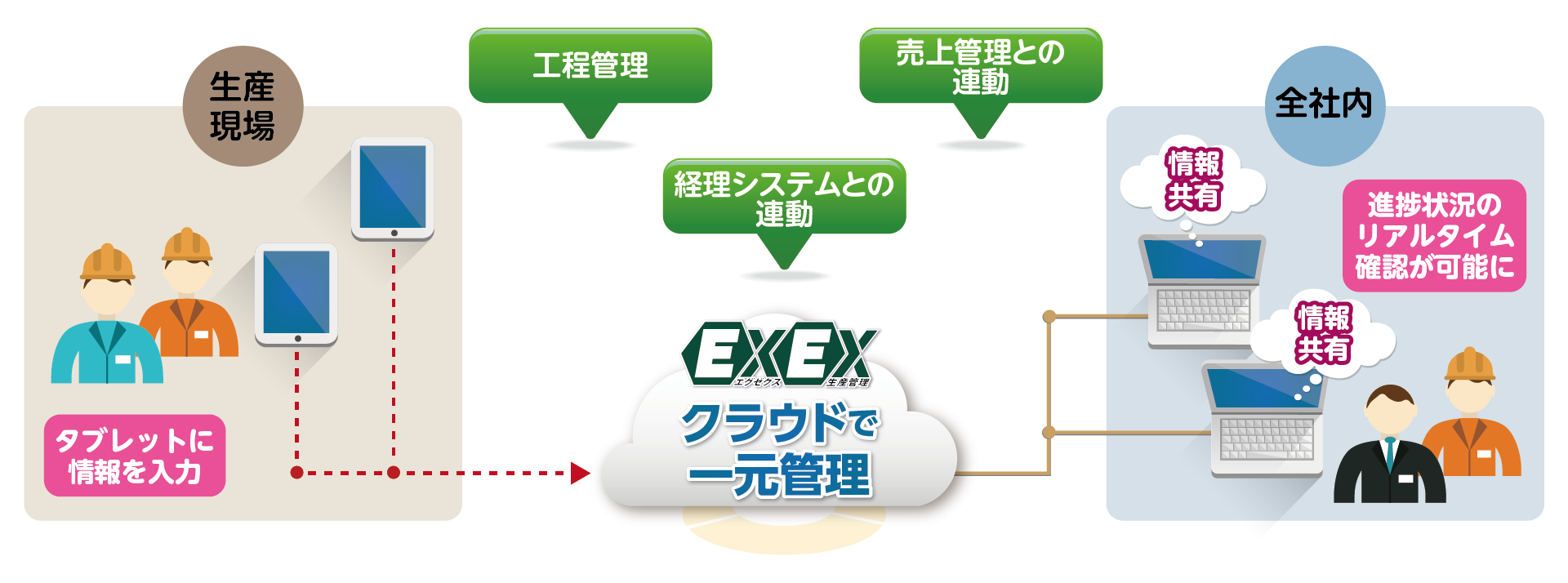
メッキ加工の工程管理がシステム化される前の現場は、加工を施す部品が紙の伝票と共にラインを進み、工程の最後に検品して伝票を回収するという昔ながらのやり方だった。一つ一つの部品の進捗具合が即座にわからない上、伝票紛失などのトラブルもある。加えて回収した伝票の内容を手入力して管理する手間もあった。また、同社で独自に構築した販売管理システムは、既に導入から年数を経て、処理に限界をきたしていた。このシステムのリニューアルをきっかけに、工程管理も含めてシステム化し、様々な不便や非効率を解消しようというのが今回の導入の目的だ。
初めての生産管理システム導入であり、情報収集はゼロからスタートした。展示会で知った数々の生産管理システムの一つが、『エグゼクス生産管理(以下、エグゼクス)』だった。検討にあたり、特に重視した条件は、クラウドとタブレットへの対応だ。シルベックの会社規模では、システムに専任のスタッフを充てる余裕はない。セキュリティーやメンテナンスを考えると自社サーバーよりクラウドにすべきであり、また、高温多湿の生産現場にパソコンの設置は困難なことから、タブレット対応も必須だった。
加えてエグゼクスが、海外の生産現場で既に数多くの導入事例があったこともポイントとなった。シルベックもタイに現地法人を持ち、いずれタイ工場での導入も検討しているからだ。これらの条件を満たして、エグゼクスのイニシャルコストは、比較した他社システムよりもコストバランスが良かった。対応に信頼が置けたことも手伝い、エグゼクスに決定した。
検査部門と営業部門で大きな成果 可視化により効率化と品質向上を実現
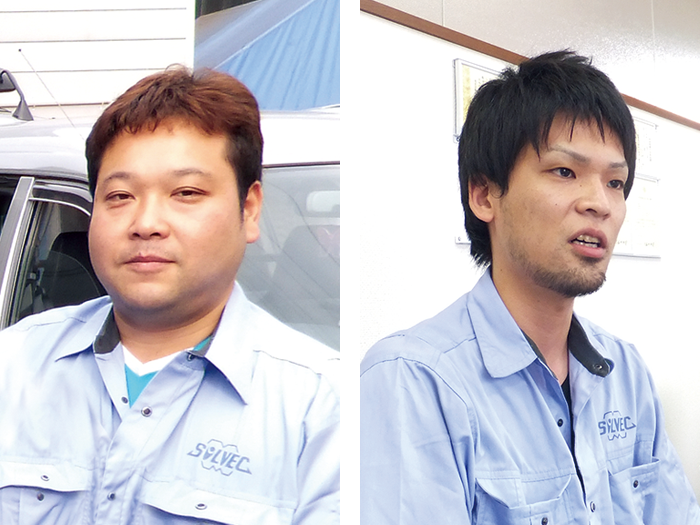
導入決定から実際の運用開始までは半年以上を要し、やや時間がかかった。「条件出しが大変でした」と、導入の実務を担った営業課の高橋晃司氏、山野寛文氏は振り返る。当時のエグゼクスはメッキ加工業の工程管理でのタブレット対応の導入事例は初めてだった。社員にヒアリングをしながら詳細を詰めていくのだが、初めてのシステム化に社員も戸惑い、当初は試作品を作っては修正するという地道な作業を積み重ねた。
そして2014年6月、いよいよ本格的に運用がスタートした。生産現場では、当初こそ操作に苦戦する社員の姿も見られたが、半年ほどで徐々に慣れていった。一方、導入効果が大きかったのは検査部門と営業部門だ。検査部門は、仕上がった部品の一つ一つを検品する部門だが、導入前は、本来業務の検品に加え、貼付されてくる伝票の入力処理も担っていた。「以前は就業時間中に検品し、伝票入力は、残業で対応することが多かった」と、山野氏は言う。エグゼクス導入により、その工程はなくなった。検査業務に集中でき、また検査で不良が出たときも、その情報をタブレットに入力することで、社員全員で共有できるようになった。工程のどの段階で、どんな不良が出ているかをリアルタイムで共有することで、改善への取り組みも進み、品質向上につながっている。
営業部門では、パソコン上で常に進捗状況を確認できるようになり、業務効率は格段にアップした。いずれは営業担当もタブレットを持ち歩き、外出先からでも顧客から状況を尋ねられた時などに、即答できる体制にすることを目指している。
可視化からすべてが始まる 近い将来、タイ工場への導入も
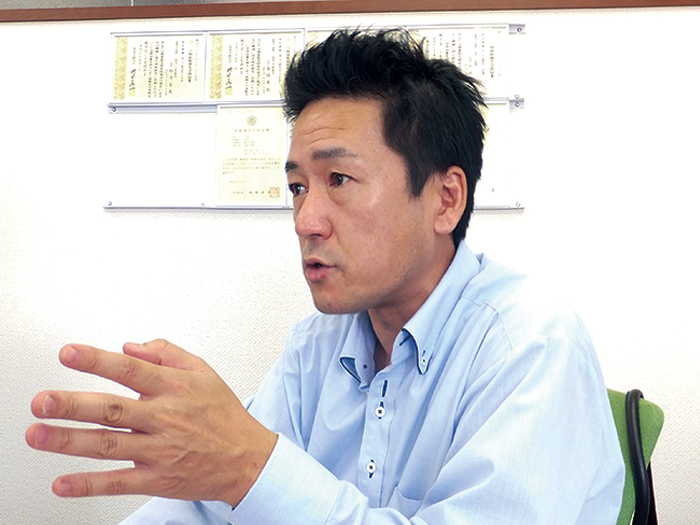
様々な効果が出ているなか、「やりたいことはもっとある」と話すのは、執行役員経営管理部部長の小野隆氏だ。例えば、各ラインの進捗状況を大型モニターで写し、リーダー全員で共有すれば、急ぎの案件が入った時も、どのラインで対応すべきかが判断できる。小野氏は言う。「結局、重要なのはすべてを可視化することです。今、会社の決算数字なども社内で公表し、全社員に会社の状況をオープンにしています。それもグラフなどでビジュアル化し、よりみんなが状況を把握しやすくすれば、問題意識の共有などにつながるでしょう。それらの取り組みの第一歩が、このシステムの導入なのです」。
今後は、加工した部品や社員の作業手順なども画像や動画で残し、品質向上や技術伝承にもつなげる考えだ。職人技として属人化しているメッキの繊細な技術を、再現性のある仕組みに変え、会社の持続的な成長を目指す。それらの大きな青写真の実現は、今回の生産の最前線のシステム化から始まると、小野氏は考えている。
そして、もう一つの大きな構想がタイ工場への導入だ。既に社員数は日本を上回り、売上も同等の水準になりつつある。今後のさらなる規模拡大を見据え、効率的な管理が不可欠だ。作業員はタイ語、マネジメント層は英語という二言語体制であり、導入にあたっては、より直感的に操作できるようにUIを工夫するなどの取り組みも必要だろう。「その辺は、タイで導入してきた実績もあり、現地に事務所も構えるシステムエグゼと二人三脚で進めていきたい」と小野氏は言う。
同業他社も同じ課題に直面 業界全体の底上げに期待
最後に、全体を通しての感想を聞いた。「同業の社長と話していると、みんな当社と同じ課題を持っているのです。今回、当社で実施した工程管理のシステム化を雛型とし、同業の他社にも導入を提案してはどうでしょうか。業界全体の発展のためにもぜひやってほしいと思います」(小野氏)。それは、製造の最前線を担う日本全国の町工場にも共通する社会課題かもしれない。エグゼクスとシステムエグゼに寄せられる期待は大きい。
※記載されている社名、製品やサービス等の名称およびロゴは一般に各社の商標または登録商標です。
※掲載内容はすべて取材当時のものであり、現在とは異なる場合があります。